Hot runner systems have become a preferred choice in the injection molding industry. The advantages of using hot runner systems go beyond just saving time—they also enhance efficiency, reduce waste, and improve the overall quality of the molded parts. But have you ever wondered exactly how hot runner systems achieve these time savings? What specific factors contribute to reducing cycle times, and how can manufacturers make these systems even more efficient to maximize their benefits?
If these questions have crossed your mind, you're in the right place! This comprehensive guide will take you through the various ways hot runner systems contribute to cycle time reduction. We’ll also explore the economic impact of hot runner systems in the injection molding process. So, without any further delay, let's dive into the details and start exploring!
Key Perks of Hot Runner Systems in Cycle Time Reduction
Hot runner systems in injection molding offer a plethora of benefits. Out of all, cycle time reduction is the most important one, contributing to improved efficiency and faster production. Here is how this happens:
Elimination of Runner Solidification Time
The hot runner system eliminates runner solidification time. In cold runner systems, molten plastic transmits through the runners to the mold cavities. Once the plastic fills the cavities, the entire system needs to cool down and solidify before the mold can be opened and parts ejected. This entire solidification process increases overall cycle time considerably.
However, hot runner systems keep the plastic within the runners in a molten state; there isn’t any need to wait for runners to cool. As soon as the part within the mold cavity cools sufficiently, the mold can be opened and the part ejected. This reduction in solidification time can lead to substantial cycle time savings, especially in high-volume production environments where even a few seconds per cycle can add up to significant productivity gain.
For instance, thousands of parts are produced in automotive manufacturing. So, the time saved with the elimination of runner solidification can considerably increase daily output and improve lead times.
Faster Cooling and Ejection
Aside from the elimination of the solidification process, hot runner systems also embrace targeted cooling. This ensures more uniform and swifter cooling of the molded parts. Additionally, because there is no need to wait for the runners to cool and solidify, the ejection process can begin immediately after the part reaches the desired temperature.
This time reduction in cooling and ejection processes is particularly evident in the manufacturing of complex parts that require precise temperature control to avoid defects. For instance, in industries such as medical device manufacturing, where tight tolerances and high-quality standards are paramount, the ability to reduce cycle times without compromising part quality is vital.
Reduction in Scrap and Material Regrind
Cold runner systems solidify along with the molded part, creating waste materials that must be removed and reprocessed. This extensive waste production not only increases cycle time but also material cost. Cycle time is increased as the scrap needs to be separated, reground, and reintroduced into the manufacturing process. Contrastingly, hot runner systems produce little to no scrap, as the runner remains molten and isn’t ejected along with the part.
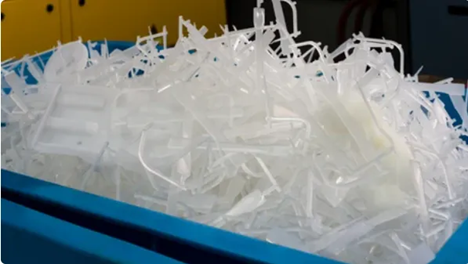
This, in turn, eliminates the need for regrinding and recycling, streamlining the material handling process and contributing to shorter cycle times. Aside from time benefit, the environmental perks are also noteworthy. This means that hot runner systems are eco-friendly and sustainable choices.
Optimized Mold Design and Multi-Cavity Molding
Want to achieve a more complex and efficient configuration? Hot runner systems' flexibility in mold design will help you do that. This flexibility is mainly evident in multi-cavity molds, where multiple parts are produced in a single cycle. In a cold runner system, each cavity would require its runner, adding to the mold's complexity and increasing the cycle time due to the additional cooling and solidification required.
In a hot runner system, the molten plastic can be evenly distributed to each cavity through the heated manifold, ensuring consistent filling and reducing the overall cycle time. This capability is particularly advantageous in industries where large volumes of identical parts are required, such as consumer goods or packaging.
Furthermore, hot runner systems enable the use of advanced gating options, such as valve gating, which allows for precise control over the flow of plastic into each cavity. This control not only improves part quality but also reduces cycle times by optimizing the filling process.
Improved Process Control and Consistency
Consistency is crucial in injection molding processes, mainly when producing large volumes of parts. It’s because a minor variation in pressure, flow rate, or temperature can lead to defects, like warping, sink marks, or short shots. All these will eventually slow down production, increasing cycle time.
Understanding this, hot runner systems offer considerable process control by maintaining consistent temperature and flow within the mold. This precision reduces the likelihood of defects, ensuring that each part meets the required specifications. This feature is very valuable in industries with stringent quality standards, such as aerospace or electronics. In these sectors, the ability to produce high-quality parts consistently and efficiently is essential for maintaining competitiveness.
The Economic Impact of Cycle Time Reduction
A faster time cycle ensures efficiency in production and offers lower operational costs, increased production capacity, and shorter lead times. Let’s explore more below.
Shorter Lead Times
In today's fast-paced world, your success in any business is determined by your quickest turnover time without compromising on quality. Customers expect quick delivery of goods, whether they are ordering a custom part for a new product or replenishing inventory for an existing one.
That said, by using hot runner systems, injection molding industries can shorten their lead times, improving customer satisfaction and enhancing their reputation for reliability. This ability to deliver products quickly can be a key differentiator in competitive markets.
Increased Production Capacity
What comes to your mind when planning to increase production capacity? Either increase labor or get additional machinery? Isn’t it? This increased capacity allows companies to respond more quickly to changes in demand, whether it’s a surge in orders for a popular product or the need to produce parts for a new product launch. So, if you are in the same boat, you can achieve significant perks with hot runner systems.
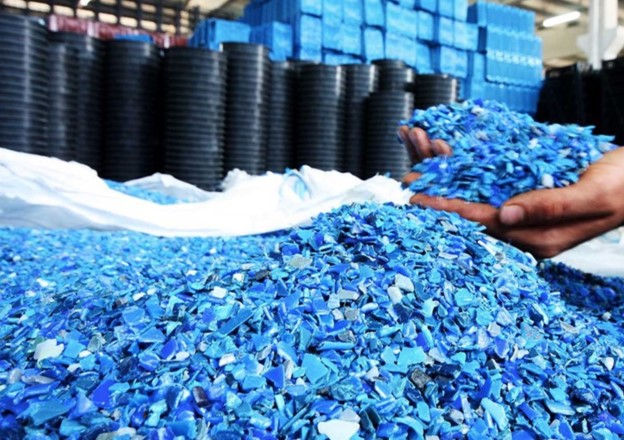
For example, during the launch of a new smartphone, manufacturers using hot runner systems can produce the necessary components more quickly, ensuring that they can meet the initial surge in demand.
Lower Operational Costs
Reducing cycle time means that manufacturers can produce more parts in the same amount of time, effectively increasing their output. This increased efficiency leads to lower per-unit costs, making the company more competitive in the marketplace, as it can offer a lower price while maintaining its profit.
Moreover, the reduction in scrap and material waste further contributes to cost savings. By minimizing material usage and reducing the need for regrinding and recycling, hot runner systems help manufacturers save on raw material costs. This can reduce a significant expense in high-volume production environments.
Where to Get the Best Quality Hot Runner Systems?
By now, you have explored the key perks of hot runner systems in cycle time reduction and the economic impacts related to it. If you want to acquire all these benefits, we recommend checking out CHRS. With two decades of experience, CHRS specializes in the research, development, and production of hot runner systems and in-mold decorating systems.
Their solutions are trusted across industries, including home appliances, automotive, packaging, office automation, and electrical tools, delivering exceptional results tailored to each sector's needs.

Some of the hot runner systems they offer are EMS‐AUTOMO SYSTEM with a screw-in type nozzle design and a special heater design to keep the temperature balanced. It also enables gate size and the nozzle's length customization and comes with a plug-in design for the spare heater without disassembly. Others on the list are PRM-ECON SYSTEM, S-DURA SYSTEM, SSV-SINGLE VALVE, TS SERIES, T-MODU SYSTEM, and PCH- T SYSTEM.
Wrapping It Up!
The impact of hot runner systems on cycle reduction is due to different factors. Everything accounts for this, from eliminating runner solidification time and speeding up the cooling process to reducing scrap and optimizing mold design. Aside from this, the economic impact of reduced cycle time is also worth mentioning. With hot runner systems, manufacturers can achieve lower costs, more production volume, and shorter lead time targets.
If you are tempted by all these perks and want to get your hands on hot runner systems, be sure to visit the CHRS website. Their exceptional quality will surely leave you impressed. Hope you found this info worth reading. Stay tuned for more helpful guides!
Kommentare