Since the development of hot runner systems (HRS), injection molding industries have benefited most. HRS are now commonly used as a replacement for cold runner systems, owing to their improved productivity. But that's not all; hot runners can benefit an injection molding industry in a plethora of ways.
If you are into getting a hot runner system for your injection molding industry but are curious about how it increases efficiency, we have covered it for you! In this comprehensive guide, we will shed light on all the perks you get to experience with HRS that together contribute to increased overall efficiency. So, without any further ado, let’s begin the journey of exploration!
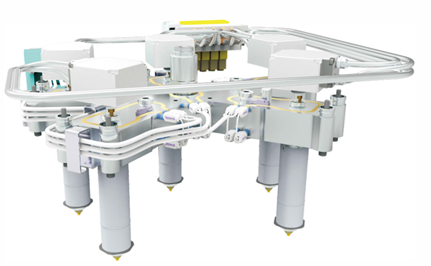
Key Factors Improving Efficiency
Below, we have covered all the key factors contributing to the increased efficiency of injection molding systems. Hop on below to have a look at them and make an informed purchase decision.
Quicker Cycle Times
When fitted with a cold runner system, injection molding undergoes multiple additional processes that hot runners help us eliminate. These include:
Cooling of the sprue and runner.
Filling of a runner during mold filling
Plastification of the melt is required to fill the cold runner.
Though the hot runner decreases the fill time only by a fraction of a second, this saved time accumulates significantly in high-speed applications. The key time-saving factor is the elimination of the additional cooling time required for the cold sprue. This issue is generally resolved with a hot sprue, costing about $800, and a temperature controller. The shorter plastification span mainly affects thin-walled high-speed molding.
That aside, HRS also has an advantage in clamp movement and the time required for the runner's ejection. This is especially true in comparison with a three-plate cold runner. Hot runner systems also reduce the required clamp stroke because the mold only needs to open enough for the part to be ejected. On the other hand, the ejection of a runner in a three-plate cold runner will require double the distance.
Optimal Part Quality
When working with cold runners, the flowing plastic loses heat to the mold plates. This heat loss causes pressure drops that may contribute to underfilled parts and sink marks. Conversely, in the case of hot runners, a balanced melt flow is achieved with constant temperature to fully pack and fill the cavities. In short, with hot runners, injection molding industries can achieve that near-ideal plastic part dimensional quality and accuracy.
Moreover, if any cavity gets damaged or wear out off the specification, it’s quite easy to prevent it from producing faulty parts by reducing the heat to its hot runner nozzle.
Melt Variations
Cold runners only create shear-induced thermal variation. Its effects are negligible on the melt and the surrounding mold temperature if the mold has enough cooling. In comparison, a hot runner introduces potential thermal variations because the material moves through and stays in different regions of the runner, each with its own temperature control. This helps molders in varying temperatures between drops and across a manifold to compensate for other problems, like observed imbalances resulting from shear-induced melt variations.
Hot runners can also create a melt variation within a given shot if the melt temperature from the injection unit is not maintained to remain the same as in the manifold. This variation can be further influenced by the volume of material in the shot relative to the volume of material in the hot runner. The larger the volume of the material, the longer its thermal history will be.
Design Flexibility
Another important hot runner advantage is its capability to locate the gate at various points on the part. By utilizing edge gating or hot tip gating, hot runners enable gate placement at the most suitable locations for optimal part aesthetic or filling. This part flexibility also extends to the mold, where flexibility in gate location helps optimize cooling, cavity orientation, and mold simplification.
Minimal Energy Usage
You might think that the hot runner uses more energy. But that's not the case. Hot runners require energy to heat up, and additional cooling is also needed to protect the mold machines from heating and counter the effect of hot runners on mold cooling. Surprisingly, they are still expected to reduce the total energy used. HRS requires minimal material to be plasticated and eliminates the use of granulators.
Improved Automation
Cold runners require additional automation equipment for proper handling. At the same time, hot runners don't require designing, building, operating, and maintaining any such equipment. It's because they eliminate the need for trimming gates and recycling cold sprue. Moreover, hot runners keep the product molten, preventing solidification. All this is conducive to production automation.
Reduced Injection Pressure
This advantage is more prominent with externally heated manifolds and drops, where the flow channels can typically be made larger than those in cold runners. However, it might become questionable when using annular flow channels, like valve gates and internally heated components are used.
Expand the Application of Injection Molding
Many advanced plastic molding processes are built on the foundation of hot runner technology. Examples include PET preform production and multi-color co-injection in the mold. Additionally, the co-injection process allows for the combination of various materials, enhancing the versatility and efficiency of manufacturing. These advancements lead to better product quality and reduced production costs. Hot runner technology also supports the development of complex and intricate designs, making it a crucial element in the evolution of injection molding applications.
Long Serving Life
The heated nozzle in hot runner systems features a standardized and serialized design with multiple optional nozzle heads and convenient interchangeability. This unique design contributes to easy customization of the hot runner for uniform heating temperature, ensuring long service life. Once invested, you won't have to worry about replacements or repairs.
Cost Saving
No doubt, the initial investment for hot runner systems is higher than for cold runners. But hot runners ensure long-term cost savings with improved cycle times, reduction in material waste, and enhanced part quality. With them, you can increase your output, minimize the need for secondary operations, reduce scrap, and eventually improve your profitability. These tempting aspects are the reasons why most injection molding industries are investing in hot runner systems.
Additional Factors That Might Contribute
Though the above factors are the main contributors to increasing the overall efficiency, certain other factors can also be considered. These include:
Reduced Clamp Tonnage: Since the hot runner doesn't provide any reactive force on the clamp, it's almost always obvious that it reduces clamp tonnage.
Cleaner Workspace: Hot runners also help maintain a cleaner environment by eliminating the need to handle certain components, such as cold runners. Their waste reduction and effective raw material usage capabilities also comply with a sustainable approach.
Elimination of Welds with Valve Gates: Hot runners feature valve gates for not only sequencing their injection but also eliminating the flaws created by a weld line.
Increased Shot Size Capability: It's unlikely that the runner's volume will cause the mold to exceed the molding machine's shot capacity, but it's still worth checking.
Utilization of Stack Molds: Molders can certainly produce stack molds with cold runners, but that's a rare case. Also, cold runner designs are very limited. Conversely, hot runners offer diverse designing and utilizing capabilities.
Where to Get Hot Runners for Your Injection Molding System?
After going through the above details, you will surely consider getting hot runners for your injection molding system. If that’s the case, we recommend checking out CHRS. They offer a diverse range of hot runners to accompany different injection molding machine designs. What sets them apart from other hot runner system manufacturers is their quality management and robust testing mechanism that ensures the delivery of top-tier products.

Whether you need EMS‐AUTOMO SYSTEM, PRM-ECON SYSTEM, T-MODU SYSTEM, or more, they offer it all at reasonable prices. Visit their website for more information regarding products and pricing.
Wrapping It Up!
Hot runner systems are capable of improving the overall efficiency of the injection molding process in different ways. From quicker cycle times, design flexibility, and melt variations to reduced injection pressure, long serving life, and more, there are a plethora of factors contributing to improved productivity. So, whether you are into cutting costs for your industry, shifting to the sustainable approach, increasing its productivity, or simply expanding its horizon, replacing cold runners with hot ones will always prove helpful.
Also, don’t forget to check out CHRS when looking for the best hot runner system companies. Their impressive collection of products and diverse range will surely help you find your desired product. In case you have any queries, you can contact their Support Team for assistance. Hope you found this article helpful. Stay tuned for more of such informative guides!
Commentaires